Comprehensive Guide: What is Porosity in Welding and Just How to avoid It
Comprehensive Guide: What is Porosity in Welding and Just How to avoid It
Blog Article
Porosity in Welding: Identifying Common Issues and Implementing Best Practices for Avoidance
Porosity in welding is a pervasive concern that frequently goes undetected till it causes considerable issues with the integrity of welds. This usual defect can jeopardize the stamina and toughness of bonded structures, positioning safety and security risks and resulting in pricey rework. By recognizing the root triggers of porosity and applying reliable prevention techniques, welders can considerably improve the high quality and integrity of their welds. In this conversation, we will certainly explore the crucial aspects adding to porosity development, analyze its detrimental impacts on weld efficiency, and talk about the very best practices that can be adopted to reduce porosity incident in welding processes.
Usual Reasons For Porosity
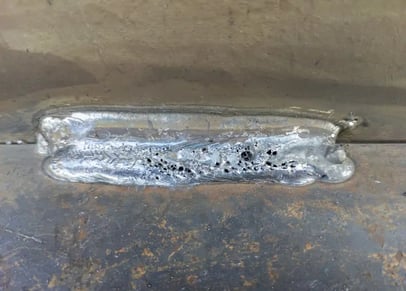
Utilizing dirty or damp filler materials can present pollutants into the weld, adding to porosity problems. To reduce these typical causes of porosity, thorough cleansing of base steels, proper shielding gas option, and adherence to optimal welding specifications are essential methods in attaining high-grade, porosity-free welds.
Influence of Porosity on Weld Top Quality

The visibility of porosity in welding can considerably endanger the structural stability and mechanical homes of bonded joints. Porosity produces gaps within the weld metal, deteriorating its general stamina and load-bearing capability. These voids function as tension concentration factors, making the weld much more vulnerable to breaking and failing under applied tons. In addition, porosity can lower the weld's resistance to rust and various other environmental aspects, additionally lessening its durability and efficiency.
Welds with high porosity levels tend to show lower effect strength and minimized ability to warp plastically prior to fracturing. Porosity can hinder the weld's capability to successfully send forces, leading to premature weld failure and prospective security risks in critical structures.
Ideal Practices for Porosity Avoidance
To boost the architectural honesty and quality of welded joints, what particular procedures can be carried out to lessen the incident of porosity throughout the welding procedure? Utilizing the appropriate welding method for the certain material being bonded, such as changing the welding angle and gun position, can even more stop porosity. Regular assessment of welds and instant remediation of any type of problems recognized throughout the welding process are necessary techniques to avoid porosity and generate top notch welds.
Significance of Proper Welding Methods
Carrying out proper welding strategies is vital in ensuring the structural stability and quality of welded joints, constructing upon the foundation of efficient porosity prevention steps. Welding methods directly affect the overall toughness and longevity of the bonded structure. One key element of correct welding methods pop over to these guys is keeping the correct warm input. Too much warm can result in boosted porosity because of the entrapment of gases in the weld pool. Alternatively, insufficient heat might result in insufficient fusion, producing possible powerlessness in the joint. Additionally, utilizing the suitable welding specifications, such as voltage, present, and take a trip speed, is vital for accomplishing audio welds with marginal porosity.
In addition, the option of welding process, whether it be MIG, TIG, or stick welding, should line up with the specific demands of the task to guarantee optimum results. Appropriate cleaning and preparation of the base metal, along with picking the appropriate filler product, are likewise important components of skillful welding techniques. By sticking to these best methods, welders her response can lessen the threat of porosity formation and produce premium, structurally sound welds.
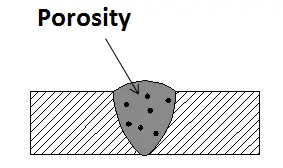
Evaluating and High Quality Control Actions
Quality assurance actions play a critical role in validating the honesty and integrity of welded joints. Examining treatments are vital to identify and protect against porosity in welding, guaranteeing the strength and toughness of the end product. Non-destructive screening approaches such as ultrasonic screening, radiographic testing, and visual evaluation are commonly employed to determine potential flaws like porosity. These strategies permit the click for source evaluation of weld high quality without endangering the honesty of the joint. What is Porosity.
Post-weld inspections, on the other hand, analyze the final weld for any issues, including porosity, and confirm that it meets defined criteria. Applying a thorough quality control plan that consists of extensive testing treatments and examinations is vital to lowering porosity problems and ensuring the total quality of welded joints.
Conclusion
To conclude, porosity in welding can be a typical issue that affects the high quality of welds. By identifying the typical root causes of porosity and implementing ideal techniques for prevention, such as proper welding methods and screening steps, welders can ensure high top quality and reputable welds. It is important to focus on prevention approaches to lessen the occurrence of porosity and preserve the honesty of welded structures.
Report this page